NVIDIA’s Push Into the Infrastructure Space Provides Opportunity for Industrial Robot OEMs
By George Chowdhury |
07 Apr 2025 |
IN-7767
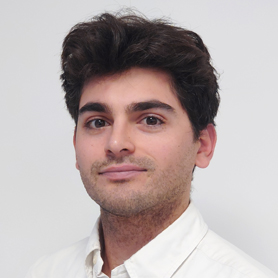
Log In to unlock this content.
You have x unlocks remaining.
This content falls outside of your subscription, but you may view up to five pieces of premium content outside of your subscription each month
You have x unlocks remaining.
By George Chowdhury |
07 Apr 2025 |
IN-7767
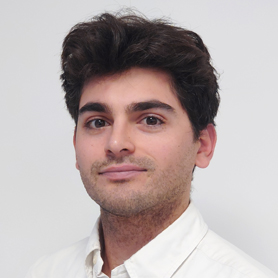
NVIDIA Ramps Up AI Roadmap with Unifying Framework for Physical AI |
NEWS |
At GTC 2025, NVIDIA outlined its vision for Artificial Intelligence (AI) as infrastructure, presenting a 4-year roadmap that will shape the role of AI in robotics and automation. The roadmap details the progression from Blackwell architecture to Rubin and eventually Feynman, each introducing improvements in AI compute efficiency, scalability, and real-time processing. These advancements support a shift in robotics from pre-programmed automation to adaptive AI-driven systems, in which models will be optimized for automated processes and continuously refine behavior based on real-world inputs. These methodologies have achieved limited uptake, to date.
NVIDIA considers Isaac Lab and Isaac Sim as key tools in this transition, enabling large-scale reinforcement learning and digital twin simulations. These technologies reduce reliance on traditional data collection and physical prototyping, making it easier to train and test AI-driven robotics. GTC showed NVIDIA’s further commitment to open-source development with the announcement of Isaac GR00T N1, which follows NVIDIA’s CES launch of Cosmos, a “world foundation model” to accelerate machine capabilities and industry collaboration.
For established robotics markets, NVIDIA’s roadmap presents both opportunities and challenges. Robotics developers will gain access to more integrated AI workflows, streamlining the process of training and deploying intelligent automation. However, manufacturers and industrial automation providers that rely on fixed-function robotics will need to adapt to a landscape where software-defined, AI-driven automation plays a larger role. However, both System Integrators (SIs) and manufacturers are uncertain of the value offering posed by AI-augmented robots.
NVIDIA's Beachheads in Commercial Robotics |
IMPACT |
NVIDIA Graphics Processing Units (GPUs) are commonplace across the mobile robot market—enabling high computational cost, mission-critical functions such as Simultaneous Location and Mapping (SLAM)—NVIDIA’s optimized software offerings, the Isaac portfolio, are beginning to find a foothold. The GTC exhibition halls showed evidence that the NVIDIA software stack is, for some, a standardized component of AI-augmented robotics. Notably, the Isaac Manipulator, used for optimizing End of Arm Tool (EOAT) orientations and actions, could be found throughout the deployments of many Collaborative Robot (cobot) solution providers. Universal Robots (UR) AI Accelerator was on display, with several UR partners leveraging the addition to demonstrate dexterous manipulation tasks relevant for manufacturing. The AI Accelerator includes an embedded NVIDIA Jetson for managing AI workloads (such as NVIDIA’s Manipulator, Perceptor, GR00T, and Cosmos products) and will accelerate the uptake of AI-augmented cobots across all industry verticals. Plausibly, it will be a matter of time before we see Jetson provided as standard for larger industrial machines; Yaskawa’s MOTOMAN NEXT Proof of Concept (PoC), which uses Isaac Manipulator on an industrial articulated arm, is indicative of this.
The announcement that the latest iteration of Isaac GR00T, N1, is to be open sourced was met with applause from the audience in attendance of Jensen Huang’s keynote. Accessibility is key to achieving greater uptake for NVIDIA’s hardware and software offerings. Open sourcing has become a common strategy to achieve penetration: Cosmos was launched as open source at CES back in January; Intrinsic’s Robot Operating System (ROS) also controls the majority of (non-industrial) robotics development projects as evidenced by NVIDIA’s Isaac ROS platform. Critically, open sourcing gives rise to developer communities enabling the organic solving of edge cases and deployment bugs, thus ameliorating NVIDIA’s support burden.
The most successful of NVIDIA’s robotics-adjacent software product is Omniverse. By leveraging the OpenUSD file format, simulation software providers have been given a readily available mechanism to project their simulations into NVIDIA’s powerful visualization tool. Again, this was evident at GTC where Rockwell Automation, Omron, and Dassault Systèmes showcased their Omniverse plugins. Although Omniverse offers impressive visuals, beneficial for wooing decision makers when pitching large projects, the software’s practical value for orchestration has yet to fully manifest. The popularity of Omniverse among established industrial manufacturing specialists is indicative of the market’s thawing sentiment toward NVIDIA’s innovations. Breaking the barrier to fully-fledged orchestration, creating AI-controlled manufacturing, is NVIDIA’s next major ambition; but it will not be easy.
OEMs Should Incorporate AI-Accelerators Directly Into Robot Controllers to Stay Ahead of Chinese Competition |
RECOMMENDATIONS |
For industrial robot Original Equipment Manufacturers (OEMs), the threat posed by China, the ousting of known-name robot brands and increasing competition in global manufacturing markets, has begun to bite into balance sheets. China’s manufacturing innovation capabilities have been hampered primarily by arguments over quality and the legacy reputation of Western vendors—increasingly, Chinese vendors are closing the gap. Incorporating AI for existing robot augmentation is likely the only way for Western OEMs to create efficiency gains and maintain, and even grow, their advantage over Chinese competitors. A major bottleneck is motion control: industrial manufacturing specialists such as Siemens, Rockwell Automation, and Schneider Electric leverage digital tools to plan and orchestrate manufacturing processes. Robot OEMs—FANUC, KUKA, and ABB—provide robots and robot controllers that the manufacturing specialists command via Programmable Logistics Controllers (PLCs) and industrial Personal Computers (PCs). Limits exist here. For example, Rockwell Automation has a close partnership with FANUC that enables streamlined control of the robot all the way up to the Rockwell Automation Emulate3D visual programming overlay. Others struggle to achieve advanced motion control due to latency and limitations when it comes to directly accessing robot controllers and tying this to digital systems. To many industrial automation specialists, the robot controller is a black box. This is a major obstacle to AI-optimization, but one that can be overcome if OEMs build AI functions into controllers, allowing engineers access via low-latency Application Programming Interfaces (APIs). Building robot controllers integrated with NVIDIA Jetson, for example, and enabling direct robot driver control and external communication with high-level industrial AI is a necessary step if NVIDIA’s AI-Infrastructure initiative is to flower.
Of course, NVIDIA isn’t the only path forward for robotics OEMs, but AI undoubtedly is. ABB has already begun to adapt its controllers for AI, incorporating the optimization benefits first seen in RobotStudio directly into ABB robot controllers. AI-acceleration can be achieved through Application-Specific Integrated Circuits (ASICs) and Field Programmable Gate Arrays (FPGAs), and many vendors will adopt these, developing their own automation solutions optimized for their robot drivers. The onus will be on NVIDIA to demonstrate that its foundation models and GPU solutions offer sufficient accessibility, power, and differentiation to court industrial robot OEMs, fastidious SIs, and industrial automation specialists. Without the buy-in of all three groups, NVIDIA will struggle to capture industrial automation markets. So far, it is seeing the most success with the final group (via OpenUSD and Omniverse), gradually gaining ground with OEMs that are becoming desperate for differentiation and optimization gains, but SIs may prove to be the hardest to crack. AI products introduce both complexity and new skill requirements to resolve deployment edge cases—SIs are inclined to circumnavigate both, as evidenced by the slow uptake of AI-augmented cobot products among Small and Medium Enterprises (SMEs). The manufacturing industry faces a skills shortage. Products adding requirements for knowledge of Machine Learning (ML) libraries and C++ will exacerbate the burden. Accessibility is key and NVIDIA is not lacking when it comes to tools for visualization. Adding to this, drag-and-drop workflows and visual process programming are sure to be a winning formula for engineers working at a high level and convincing decision makers of Return on Investment (ROI).
The final slide of the GTC 2025 keynote highlighted NVIDIA’s forecast Total Addressable Market (TAM) for Physical AI: US$50 trillion. To unlock anything close to this value and continue to keep its hands clean by remaining a platform, rather than a solution provider, NVIDIA must win buy-in from the three groups listed above. For their part, industrial robot OEMs, feeling the squeeze from China, must adopt AI or risk falling further behind; ensuring closer ties with NVIDIA appears to be a win-win for all concerned.
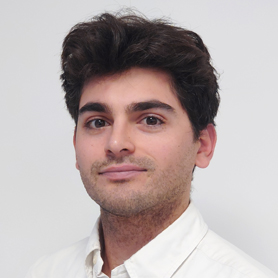